Concrete is the foundation of our modern world, from towering skyscrapers to the sidewalks we walk on. But not all concrete is created equal. The secret to unlocking its full potential lies in what we add to the basic mix. This article is your definitive guide to understanding concrete additives, the special ingredients that can dramatically increase strength, improve workability, and ensure long-term durability. As a factory owner with over a decade of experience in specialized building materials, I’ve seen firsthand how the right additive can transform a project. I’m here to share that knowledge with you, so you can make informed decisions, avoid common pitfalls, and build with confidence. Whether you’re a developer, a precast manufacturer, or a procurement officer like my friend Mark Thompson in the USA, this guide will provide the clarity you need.
What Are Concrete Additives and Why Are They Essential?
At its core, concrete
is a simple mixture of portland cement
, water, sand, and a coarser aggregate
like gravel. When these are combined, a chemical reaction called hydration
begins, causing the concrete
to harden and gain strength. However, the demands of modern construction often require performance characteristics that this basic mix
can’t provide on its own. This is where a concrete additive
, also known as an admixture
, comes into play. These are materials, other than the basic four, that are added to the concrete mix
immediately before or during mixing to modify its properties.
Think of it like baking a cake. Flour, sugar, and eggs make a cake, but adding vanilla extract, baking powder, or chocolate chips changes its flavor, texture, and rise. Similarly, additives are used
to enhance the performance of concrete
. They can make fresh concrete
flow more easily, speed up or slow down its hardening set time
, reduce costs, and, most importantly, increase the strength and durability
of the final product. Using the correct additive
is not just about improving the concrete
; it’s about ensuring the long-term safety, resilience, and efficiency of the entire structure. From a small residential foundation to a massive bridge, the right concrete additives
are critical for achieving optimal concrete quality
.
The goal is to engineer the concrete
for its specific purpose. A concrete
slab in a freezer warehouse has very different needs than a high-rise column in a hot climate. An additive
allows us to customize the concrete mix
to meet these challenges, improving everything from its ability to resist freeze-thaw
cycles to its ultimate compressive strength. In my business, we specialize in advanced building materials
where additives are not just beneficial but fundamental to the product’s existence, proving just how transformative these ingredients can be.
How Do Superplasticizers Enhance Concrete Mix Workability and Fluidity?
One of the most impactful types of additives
is the water-reducing
admixture
, particularly the high-range versions known as superplasticizers
. A fundamental rule in making concrete
is that strength is inversely related to the water-cement ratio. Less water means stronger, more durable concrete
. The problem? A concrete mix
with very little water is stiff, difficult to place, and won’t properly fill forms or surround reinforcement
. It has poor workability
. This is the problem superplasticizers
solve.
When added to concrete
, these powerful admixtures work on a particle level. They wrap around the cement
particles, giving them a strong negative charge that causes them to repel each other. This action breaks up clumps of cement
, releasing the water trapped inside and dramatically increasing the fluidity
of the mix
without adding a single extra drop of water. The result is a flowing, self-leveling concrete
that is incredibly easy to pour and finish. This allows you to significantly reduce the amount of water
needed, leading to a much lower water-cement
ratio and, consequently, high-strength
concrete
.
For procurement officers like Mark, who oversee projects with complex engineering requirements, this is a game-changer. Imagine trying to pump concrete
to the top of a 50-story building or ensuring it perfectly encases a dense cage of steel reinforcement
. A stiff mix
would be impossible. Superplasticizers
make it possible, ensuring the concrete
reaches every corner and void, eliminating defects and guaranteeing the structural integrity of the element. They allow you to make concrete
that is both incredibly strong and easy to handle.
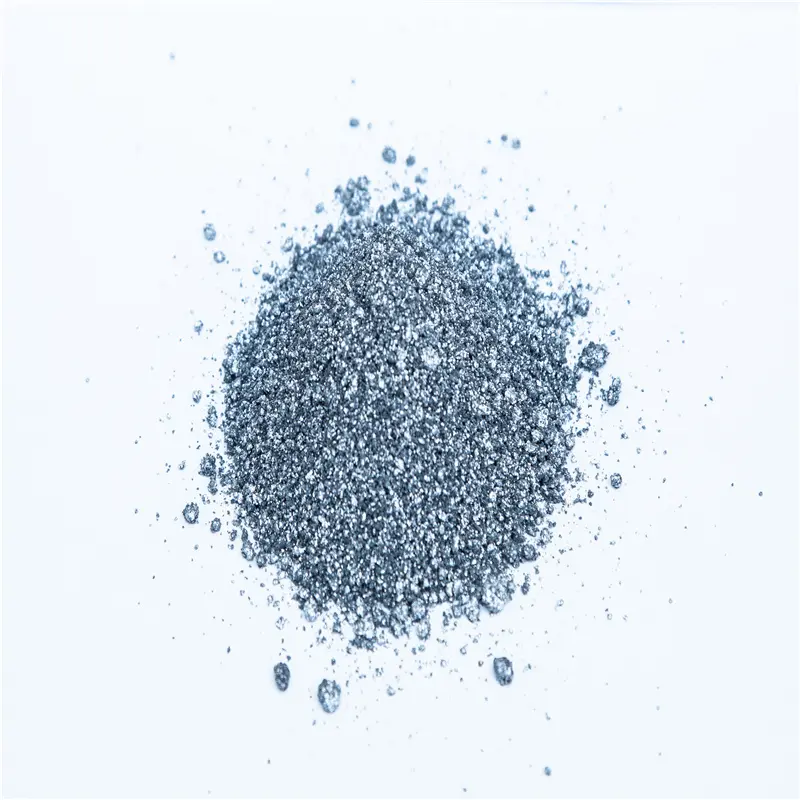
Can You Really Increase Early Strength with an Accelerator?
Absolutely. In construction, time is money. The faster concrete
can gain strength, the faster forms can be stripped, and the sooner the next phase of construction can begin. An accelerator
is an admixture
designed to do just that. It speeds up the rate of cement
hydration
, reducing the set time
and promoting rapid development of early strength
. This is particularly vital in cold weather conditions, where low temperatures can significantly slow the chemical reactions that give concrete
its strength, leaving it vulnerable to damage from freezing.
The most common and cost-effective accelerator
is calcium chloride
. It’s highly effective at getting the concrete
to harden quickly. However, a major word of caution is needed here. Chloride
ions are extremely corrosive to steel. Therefore, calcium chloride
should never be used in reinforced concrete
, prestressed concrete
, or any concrete
that will contain embedded metal, as it will lead to the rusting and degradation of the reinforcement
over time. For these applications, non-chloride accelerators are available and are the only safe option.
An accelerator
allows a precast concrete
plant to increase its daily output by freeing up molds more quickly. On-site, it means a slab poured in the afternoon can be hard enough to walk on by the next morning. It’s a powerful tool for schedule-driven projects. But, like any powerful tool, it must be used correctly. Understanding the chemistry and potential downsides, especially regarding calcium
and chloride
, is key to using an accelerator
effectively and safely to make concrete
that performs well both today and for decades to come.
What Is the Role of a Retarder in Controlling the Concrete Set Time?
Just as we sometimes need concrete
to harden faster, there are many situations where we need to slow it down. This is the job of a retarder
. A retarder
is a concrete additive
that slows down the chemical reaction of hydration
. By delaying the initial set time
, it keeps the concrete
in a plastic, workable state for a longer period. This is incredibly valuable in a few key scenarios that my international clients face regularly.
First, hot weather concreting. High ambient temperatures naturally speed up the concrete
setting process, sometimes so much that the mix
begins to harden in the truck before it can even be poured. A retarder
counteracts this effect, providing the necessary window of time to place and finish the concrete
properly. Second, long-haul deliveries. If a concrete
plant is far from the job site, a retarder
ensures the mix
arrives fresh and ready to pour, not half-hardened. This directly addresses a major pain point for project managers: logistics and timing.
Finally, for large, continuous pours, such as a massive foundation or a bridge deck, a retarder
is essential. It prevents "cold joints," which are weak points that form when one layer of concrete
hardens before the next layer is poured on top of it. By keeping the entire mass workable, a retarder
helps ensure the concrete
is monolithic and structurally sound. It provides control, which is crucial for high-stakes concrete
work, preventing costly mistakes and ensuring a high-quality final product.
How Does Fiber Reinforcement Improve Concrete Toughness?
Traditional non-reinforced concrete
is very strong under compression (squeezing forces) but very weak under tension (pulling forces). When it’s pulled, it tends to crack
and fail suddenly. This is why we add steel rebar. But there’s another way to reinforce
concrete
on a microscopic level: adding fibers. Fiber
is a type of additive
that involves mixing small, discrete fibers directly into the concrete
. These can be made of steel, glass, synthetic polymers, or natural materials.
Instead of a few large steel bars, you get millions of tiny fibers distributed in every direction throughout the concrete mix
. While they don’t eliminate cracking entirely, they play a crucial role once a micro-crack forms. The fibers bridge the crack
, holding the concrete
together and requiring more energy to pull it apart. This dramatically increases the concrete
‘s tensile strength
and, more importantly, its toughness
—its ability to absorb energy and deform without shattering. It changes the failure mode from brittle to a more ductile, gradual one.
This enhanced crack resistance
is invaluable for applications like industrial floors, pavements, and precast products, where shrinkage
cracks are a common concern. A fiber
-reinforced concrete
slab is more durable and resilient against impacts and daily wear and tear. It’s a simple but effective way to make concrete stronger and more durable
by tackling its inherent weakness to tensile forces head-on. It’s about building in resilience from the inside out, improving the overall strength and toughness
of the material.
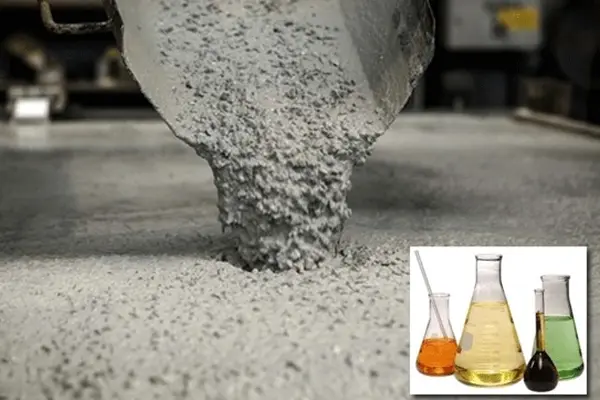
What Are Mineral Admixtures and How Do They Reinforce Concrete?
While chemical additives to concrete
like superplasticizers and retarders modify the hydration reaction, mineral admixtures
become a part of the concrete
itself. These are fine, siliceous materials, often called pozzolans
or supplementary cementitious materials
(SCMs), that are used to replace a portion
of the portland cement
in a mix
. The most common are fly ash
(a byproduct of coal power plants), slag
cement (a byproduct of steel manufacturing), and silica fume
(a byproduct of silicon metal production).
These materials as additives
contribute to strength through a secondary reaction. The initial hydration
of cement
produces a byproduct called calcium hydroxide
, which doesn’t contribute much to strength. Mineral admixtures
are pozzolanic, meaning they react with this calcium hydroxide
and water to form more of the strong, durable calcium silicate hydrate—the same compound that gives concrete
its strength in the first place. This reaction is slower, so it doesn’t boost early strength
, but it leads to a much denser, less permeable, and ultimately stronger concrete
in the long run.
Using mineral admixtures
offers a triple benefit. First, it can significantly increase
the ultimate strength and durability of concrete
. Second, by making the concrete
denser, it improves its resistance to chemical attack and water penetration. Third, it enhances sustainability
. Since fly ash
and slag
are recycled industrial byproducts, using them reduces the demand for new cement
production, which is an energy-intensive process. For developers and manufacturers focused on green building standards, incorporating SCMs is a smart way to increase the sustainability
and performance of their concrete
. It’s this same principle of using fine pozzolanic materials that helps create the strong, lightweight matrix in our advanced building products, such as our Aluminium pastes for aerated concrete, which are essential for producing high-quality aerated concrete.
What About Air-Entraining Additives for Durability?
For any concrete
exposed to the elements, especially in colder climates like the Northern USA, Canada, or Europe, one of the biggest threats is the freeze-thaw
cycle. When water trapped in the pores of concrete
freezes, it expands by about 9%, creating immense internal pressure that can break the concrete
apart from the inside out. This is where an air-entraining admixture
becomes one of the most important additives
for durability.
This additive
works by creating a stable network of billions of microscopic air bubbles
throughout the concrete
. These tiny voids act as pressure-relief valves. When water in the surrounding capillaries freezes and expands, it can move into these empty air bubbles instead of exerting pressure on the concrete
itself. This provides a dramatic resistance to freeze-thaw cycles
, preventing the surface scaling and internal cracking that would otherwise destroy the concrete
over a few winters.
Beyond freeze-thaw
resistance, air entrainment also offers other benefits. It improves the workability
of the fresh concrete mix
, making it easier to place and finish. It also reduces segregation
(where heavy aggregate
settles) and bleeding (where water rises to the surface). For anyone building in a region with freezing temperatures, an air-entraining admixture
isn’t optional; it’s a mandatory requirement to ensure the concrete
will last. It is a fundamental tool used to increase
the service life of exterior concrete
.
How Do You Choose the Right Admixture for Your Concrete Mix?
With so many types of additives
available, selecting the right one—or the right combination—can seem daunting. The choice always comes down to the specific needs of your project. As a manufacturer, I advise my clients to approach this systematically. There is no one-size-fits-all solution; the key is to match the admixture
to the desired outcome and the environmental conditions.
Here’s a simple decision-making framework:
If your primary goal is… | Consider this additive… | Because it… |
---|---|---|
High Strength | Superplasticizer (water-reducer ) |
Lowers the water-cement ratio, which is key to making concrete stronger . |
Durability in Cold Climates | Air-Entrainer | Creates air pockets to protect the concrete from freeze-thaw damage. |
Fast-Track Construction | Accelerator | Speeds up the set time and development of early strength . |
Hot Weather / Long Pours | Retarder | Slows down setting to provide more workability time. |
Crack & Impact Resistance | Fiber Reinforcement | Adds toughness and controls shrinkage cracking. |
Long-Term Strength & Sustainability | Mineral Admixtures (fly ash , slag ) |
Enhances durability of concrete and reduces the cement content . |
The most critical step is to conduct trial mixes. Before committing to a large-scale pour, test your proposed concrete mix
in a lab or on a small scale. This allows you to verify its properties—strength, set time
, and workability
—and make adjustments. Compatibility is also key; some additives
don’t work well together. Partnering with a knowledgeable supplier who can provide clear technical data and guidance is essential to improve the strength
and performance of your final product. This precision engineering is the same philosophy we apply to our pre-made materials like AAC Block, which are designed for consistent, reliable performance on the job site.
Beyond Strength: What Other Benefits Do Concrete Additives Offer?
While the quest to increase strength
is often what leads people to explore additives
, their benefits extend far beyond that single metric. A holistic view reveals that additives
are about total performance enhancement, making the concrete
not just stronger, but better in almost every way.
Let’s look at some of the other crucial advantages:
- Economic Benefits: Using
superplasticizers
tomake concrete
with lesscement
or usingmineral admixtures
likefly ash
to replace a portion of expensiveportland cement
can lead to significant cost savings on large projects. - Improved Quality & Aesthetics: Additives can reduce surface blemishes, control color, and create a smoother, more uniform finish. They also reduce the risk of defects like honeycombing and
segregation
. - Enhanced Durability: Beyond
freeze-thaw
, certainadditives
can makeconcrete
more resistant to chemical attacks, sulfate attacks, and alkali-silica reactions, significantly extending the structure’s service life. - Specialized Properties: This is where innovation truly shines. Additives can be used to create entirely new classes of
concrete
. For example, gas-forming agents are a specialadditive
used to create lightweight, cellularconcrete
with excellentinsulating properties
. This is the technology behind our ALC Wallboard, which provides both structural support and thermal insulation in one material. Otheradditives
can create corrosion-inhibitingconcrete
,shrinkage
-compensatingconcrete
, and even water-proofconcrete
.
As a Manufacturer, What Should You Look For in a Supplier?
For a procurement officer like Mark, the quality of the final construction project depends heavily on the consistency of the raw materials. A batch of concrete
that fails to perform as specified can lead to catastrophic delays and costs. Therefore, choosing the right supplier for your concrete additives
or other building materials
is just as important as choosing the right additive
itself. As a factory owner who exports globally, I know what my most discerning clients look for.
First and foremost is Quality Consistency. You need a supplier who can guarantee that the product you receive in July is identical in performance to the one you received in January. This requires robust quality control, regular testing, and certifications like ISO 9001. Ask for technical data sheets (TDS) and material safety data sheets (MSDS) for every product.
Second is Technical Expertise and Support. Your supplier shouldn’t just be a salesperson; they should be a partner. They should understand how their additive
interacts with different types of cement
and aggregates and be able to help you troubleshoot your concrete mix
. This is where dealing directly with a Professional Water-based Aluminum Powder Slurry Factory like ours provides a huge advantage. We have the in-house expertise to answer technical questions and ensure our product is right for your application. Clear communication and responsiveness are non-negotiable—they are the antidote to the pain points of shipment delays and quality concerns. A reliable supplier helps you build with confidence, knowing every component is up to standard.
Key Takeaways
Navigating the world of concrete additives
is key to unlocking the full potential of this incredible material. Here are the most important things to remember:
- Additives are Essential: They are not just optional extras; they are critical tools for engineering modern
concrete
to meet specific performance, durability, andworkability
requirements. - Choose Based on Your Goal: Select
additives
strategically. Usesuperplasticizers
for high strength, retarders for hot weather, accelerators for speed, and air-entrainers forfreeze-thaw
durability. - Fibers Add Toughness:
Fiber
reinforcement is a game-changer for improvingcrack resistance
and preventing brittle failure inconcrete
. - Minerals Add Long-Term Strength:
Mineral admixtures
likefly ash
andslag
not onlyincrease the strength and durability
over time but also improve thesustainability
of yourconcrete mix
. - Test and Verify: Always conduct trial mixes to ensure your
concrete
performs as expected before a large-scale application. - Partner with Experts: Your supplier’s reliability is paramount. Work with manufacturers who guarantee quality consistency and provide excellent technical support to avoid project delays and ensure a successful build.
Post time: 6 月-25-2025