Autoclaved Aerated Concrete, commonly known as AAC blocks, represents a significant advancement in building material technology. These lightweight concrete blocks are transforming the construction industry, offering a compelling alternative to traditional brick and conventional concrete blocks. If you’re involved in construction, development, or building material distribution, understanding the unique properties, benefits, and considerations of AAC blocks is crucial. This article delves deep into the world of Autoclaved Aerated Concrete, exploring its manufacturing process, comparing it with conventional materials, highlighting its numerous advantages, addressing potential disadvantages, and showcasing its versatile applications. Discover why this innovative material is rapidly gaining popularity worldwide and how it can contribute to more efficient, sustainable, and cost-effective building projects.
1. What Exactly are AAC Blocks (Autoclaved Aerated Concrete)?
AAC block is short for Autoclaved Aerated Concrete block, a highly versatile and lightweight building material. Invented in the mid-1920s by the Swedish architect and inventor Dr. Johan Axel Eriksson, AAC blocks were developed to meet the demand for a building material that offered the structural benefits of concrete while also providing good thermal insulation and being easier to handle than traditional brick or concrete blocks. It’s essentially a precast foam concrete material, known for its distinctive lightweight and porous nature.
The composition of Autoclaved Aerated Concrete typically includes fine aggregates like quartz sand or fly ash, cement, lime, gypsum, water, and an expansion agent, most commonly aluminum powder. When these ingredients are mixed, a chemical reaction occurs between the aluminum powder and the calcium hydroxide (from cement and lime), producing hydrogen gas. This gas creates millions of tiny, evenly distributed air pockets within AAC blocks, similar to the structure of a sponge, which is key to its lightweight property and excellent insulation capabilities.
Unlike traditional concrete which cures at ambient temperatures, AAC blocks undergo a high-pressure steam curing process in a machine called an autoclave. This autoclave process is critical; it accelerates the curing and induces chemical changes that result in AAC material possessing high strength, durability, and dimensional stability, distinguishing it from other forms of lightweight concrete. The resulting AAC blocks are non-toxic, workable like wood (they can be easily cut, drilled, and shaped), and offer superior performance characteristics compared to many conventional construction materials.
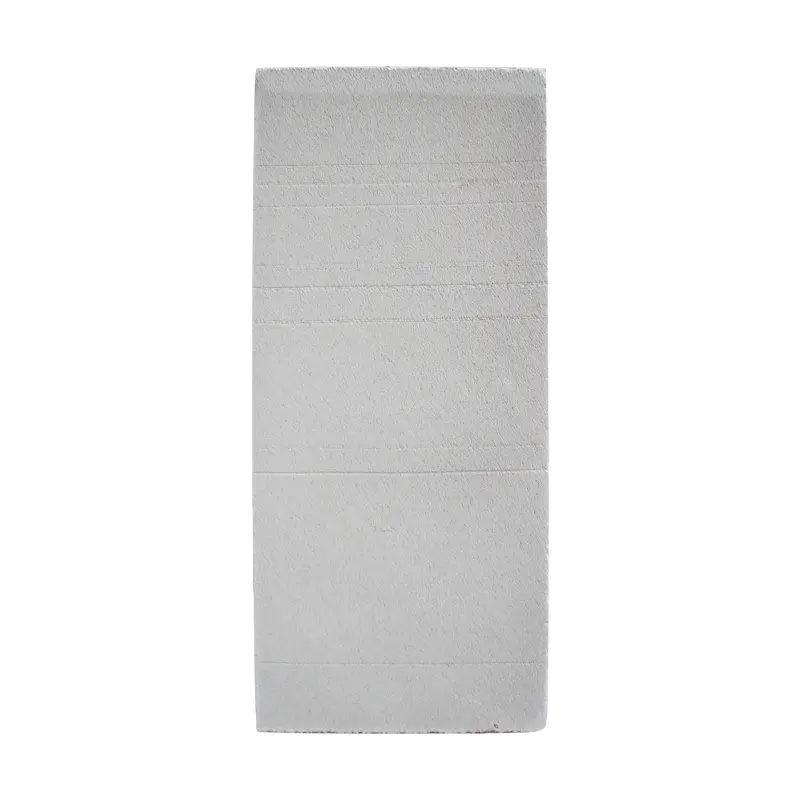
2. How are AAC Blocks Manufactured? The Critical Role of the Autoclave.
The production of AAC blocks is a precise industrial process involving several key stages. It begins with the careful selection and preparation of raw materials: fly ash (or finely ground quartz sand), cement, lime, gypsum, and water are proportioned and mixed to form a slurry. A small, precisely measured amount of expansion agent, typically high-quality aluminium pastes for aerated concrete, is added to this slurry. This aluminum reacts with the alkaline elements in the cement and lime mixture, generating hydrogen gas bubbles.
This reaction causes the slurry to expand significantly within large molds, creating a "cake" filled with countless tiny, non-connected air pores – the defining characteristic of AAC blocks. This expansion process is carefully controlled to achieve the desired density and porous structure. Before the cake fully hardens, it reaches a consistency where it can be precisely cut into blocks or panels of required sizes and strengths using specialized cutting wires. This ensures dimensional accuracy, which is crucial for efficient construction and minimizing mortar usage.
The final and most critical stage is curing in an autoclave. The cut blocks are placed inside this large, pressurized steam chamber (the autoclave) for several hours (typically 10-12 hours) under high pressure (around 12-14 bar) and temperature (around 190-200°C). This autoclave curing process facilitates a secondary hydration reaction (tobermorite formation), giving the AAC blocks their characteristic high strength, low shrinkage, and overall durability. The autoclave process ensures a complete and uniform cure throughout the material, resulting in a stable and reliable building material.
3. Why are AAC Blocks Considered Lightweight Yet Surprisingly Strong?
The secret to the AAC block‘s unique combination of being lightweight yet robust lies in its manufacturing process and resulting structure. The introduction of the expansion agent (aluminum powder) creates a vast network of tiny, disconnected air bubbles throughout the material. These pores typically make up about 70-80% of the volume of an AAC block, drastically reducing its density compared to traditional concrete blocks or clay bricks. An AAC block is typically 3 to 5 times lighter than a traditional brick or concrete block of the same size.
Despite this porous structure, AAC blocks possess remarkable compressive strength, suitable for many structural applications, including load-bearing walls. This strength doesn’t come from density, but from the solid matrix structure formed during the autoclave curing process. The high-pressure steam curing creates a crystalline structure (tobermorite) that binds the cement, lime, and sand/fly ash particles together effectively. This robust micro-structure provides the necessary compressive strength even with the high porosity.
Therefore, AAC blocks are lightweight enough to significantly reduce the dead load of a building (leading to savings in foundation and structural frame costs) while still offering sufficient compressive strength for safe and durable construction. This combination makes AAC blocks an incredibly efficient building material. The strength-to-weight ratio of AAC blocks is considerably better than that of traditional masonry units like bricks.
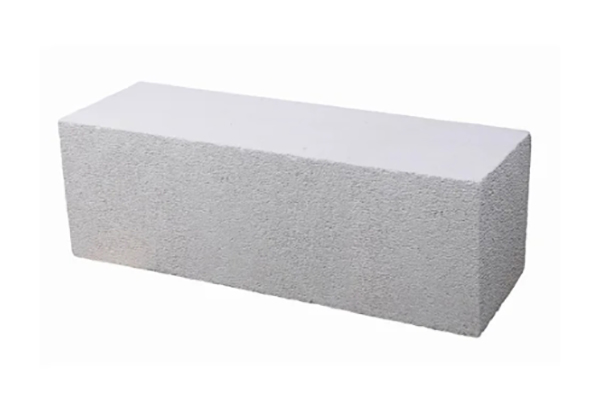
4. AAC Blocks vs. Traditional Clay Bricks vs. Concrete Blocks: Which is Better for Your Construction Project?
Choosing the right masonry unit is critical for any construction project. Let’s compare AAC blocks with traditional clay bricks (like red brick) and conventional concrete blocks across key parameters:
Feature | AAC Block | Traditional Clay Brick | Conventional Concrete Block |
---|---|---|---|
Weight | Very Lightweight (approx. 550-650 kg/m³) | Heavy (approx. 1600-1900 kg/m³) | Heavy (approx. 1900-2200 kg/m³) |
Size | Larger, more precise dimensions | Smaller, less uniform | Moderate size, moderate uniformity |
Thermal Insulation | Excellent thermal insulation (low conductivity) | Poor insulation | Moderate insulation |
Compressive Strength | Good (typically 2.5-7 N/mm²) | Good to High (varies widely) | Moderate to High (varies widely) |
Fire Resistance | Excellent (non-combustible, up to 4-6 hours) | Good (non-combustible) | Good (non-combustible) |
Construction Speed | Faster (larger units, less mortar) | Slower (smaller units, more joints) | Moderate speed |
Mortar Consumption | Low (thin-bed mortar) | High | Moderate |
Workability | Excellent (easy to cut, shape, chase) | Moderate (can be cut, but harder) | Poor (difficult to cut/shape) |
Water Absorption | Low water absorption (due to non-connected pores) | High (especially for red clay brick) | Moderate |
Cost (Material) | Initially higher per unit, but fewer needed | Lower per unit, but many needed | Moderate |
Cost (Overall) | Often lower total construction cost | Can be higher due to labor/time | Moderate |
Sustainability | Good (less material, energy saving) | Moderate (high firing energy) | Moderate (high cement content) |
Key Takeaways from the Comparison:
- AAC blocks excel in thermal insulation, lightweight properties, fire resistance, and construction speed.
- Traditional bricks offer aesthetic appeal and familiarity but lag in insulation and construction efficiency. They are also significantly heavier.
- Concrete blocks provide strength but are heavy and offer only moderate insulation and workability compared to AAC blocks.
The choice depends on project priorities. For energy-efficient buildings, faster construction, and reduced structural load, AAC blocks present a compelling advantage over traditional brick and concrete block alternatives.
5. What Are the Major Advantages of Using AAC Blocks in Modern Construction?
The unique properties of AAC blocks translate into numerous benefits for builders, developers, and building occupants. Here are some of the primary advantages of AAC blocks:
- Lightweight: As mentioned, AAC blocks are lightweight (around 1/4th to 1/5th the weight of traditional concrete). This reduces the dead load on foundations and structural frames, potentially leading to significant savings in steel and concrete for the structure. It also makes handling and transportation easier and safer.
- Excellent Thermal Insulation: The millions of trapped air pores give AAC blocks very low thermal conductivity. This keeps buildings cooler in summer and warmer in winter, drastically reducing the need for artificial heating and cooling, thus lowering energy bills and improving comfort. This is a major benefit for energy-efficient construction.
- Superior Fire Resistance: AAC material is inorganic and non-combustible. It offers excellent fire resistance, typically providing a fire endurance rating of 4 hours or more for a standard 100mm thick wall, significantly higher than traditional brick or concrete block walls. This enhances building safety.
- Acoustic Insulation: The porous structure of AAC blocks also helps to absorb sound waves, providing better acoustic insulation than denser materials like brick or concrete. This leads to quieter interiors, ideal for residential buildings, hospitals, hotels, schools, villas, stores, etc.
- Faster Construction: AAC blocks are larger than traditional bricks (often 8-10 times the size). This means fewer units are needed per square meter of wall, and fewer joints need mortar. Combined with their ease of handling and workability, this significantly speeds up the construction time.
- Dimensional Accuracy: Manufactured to precise dimensions (thanks to the cutting process before the autoclave stage), AAC blocks allow for thin-bed mortar application (2-3mm joints), reducing mortar consumption by up to 60-70% compared to conventional masonry. This also results in straighter walls and reduces the need for thick plaster coats.
- Workability: AAC blocks can be easily cut, sawn, drilled, nailed, and routed using standard woodworking tools. This simplifies the installation of electrical conduits, plumbing pipes, and fixtures, reducing labor time and costs during finishing stages.
- Durability and Strength: Despite being lightweight, the autoclave process ensures AAC blocks have good compressive strength and are resistant to rot, pests, termites, and mold. They offer long-term durability for a durable building.
- Moisture Resistance: While porous, the pores (macro-pores) in AAC blocks are non-connected (closed-cell structure), resulting in relatively low water absorption through capillary action compared to clay bricks. This helps prevent dampness issues.
- Eco-Friendly: Often made with industrial waste products like fly ash, requiring less energy to produce than bricks, and contributing significantly to energy savings during the building’s lifetime, AAC blocks are considered a relatively sustainable building material.
6. Are There Any Disadvantages or Limitations to Using AAC Blocks?
While AAC blocks offer many advantages, it’s also important to consider their potential limitations or advantages and disadvantages:
- Brittleness: Compared to clay bricks, AAC blocks can be more brittle and susceptible to chipping or damage during careless handling or transportation. Proper care is required on the construction site.
- Lower Compressive Strength than Dense Concrete: While adequate for most walling applications (both load-bearing and non-load-bearing), the compressive strength of standard AAC blocks is generally lower than that of high-strength concrete blocks or engineered bricks. Specific structural design calculations are necessary, especially for high-load applications.
- Cost: The initial purchase price per AAC block can sometimes be higher than a single traditional brick or concrete block. However, this is often offset by savings in labor, mortar, structural support, construction time, and long-term energy costs. A total project cost analysis is recommended.
- Need for Protective Finishing: Due to their porous nature (even with low capillary action), AAC blocks used for exterior walls require a protective finish (like polymer-modified plaster, cladding, or paint) to prevent long-term weathering and excessive moisture ingress, especially in rainy climates. Interior walls also typically require plaster or drywall finishes.
- Specialized Mortar: AAC blocks perform best with thin-bed mortar, which is specifically designed for this purpose. While readily available, it differs from traditional thick-bed cement mortar used for bricks, requiring masons to adapt their techniques.
- Potential for Cracking if Not Installed Correctly: Like any masonry system, improper installation (e.g., inadequate expansion joints, incorrect mortar application, differential settlement) can lead to cracking. Adherence to manufacturer guidelines and good construction practices is essential.
Understanding these points allows for proper planning and mitigation, ensuring the successful application of AAC blocks in construction.
7. Where Can You Effectively Use AAC Blocks in Building Construction (Walls, Floors, etc.)?
The versatility of AAC blocks makes them suitable for a wide range of applications in the construction industry. Their unique properties lend themselves well to various building elements:
1. Exterior Walls: AAC blocks are widely used for exterior wall construction, both load-bearing and non-load-bearing (infill walls in framed structures). Their excellent thermal insulation significantly contributes to the building’s overall energy efficiency. A proper external rendering or cladding system is necessary for weather protection. ALC panels (Autoclaved Lightweight Concrete panels), which are larger reinforced versions, are also commonly used for exterior wall systems.
2. Interior Walls / Partition Walls: Their lightweight nature, ease of installation, and good acoustic performance make AAC blocks ideal for internal wall partitions (lpar;interior) wall,,). They can be erected quickly and easily accommodate electrical and plumbing services.
3. Fire Separation Walls: Due to their excellent fire resistance ratings, AAC blocks are frequently specified for fire-rated separation walls between units in multi-family housing, commercial buildings, or different functional areas within a building.
4. Acoustic Barriers: The sound dampening properties make AAC blocks suitable for walls where noise reduction is important, such as in hospitals, hotels, schools, and apartment buildings.
5. Floors and Roofs (using AAC Panels): While standard AAC blocks are primarily for walls, reinforced AAC panels (ALC panels) are often used for floor and roof slab systems. These panels offer the same benefits of light weight and insulation while providing the necessary structural capacity for horizontal spans.
6. Diverse Building Types: AAC blocks are suitable for virtually all types of buildings, including:
- Civil housing,, apartments, villas,,
- Commercial buildings: stores,, supermarkets etc.
- Institutional buildings: schools,, hospitals,,
- Hospitality: hotels,,
- Industrial constructions,, warehouses
- Public facilities,,
Their adaptability makes them a go-to building material for modern, efficient construction. Whether it’s a simple partition or a complex exterior wall system, AAC blocks offer a reliable solution. You can even find details and price specific to your project needs.
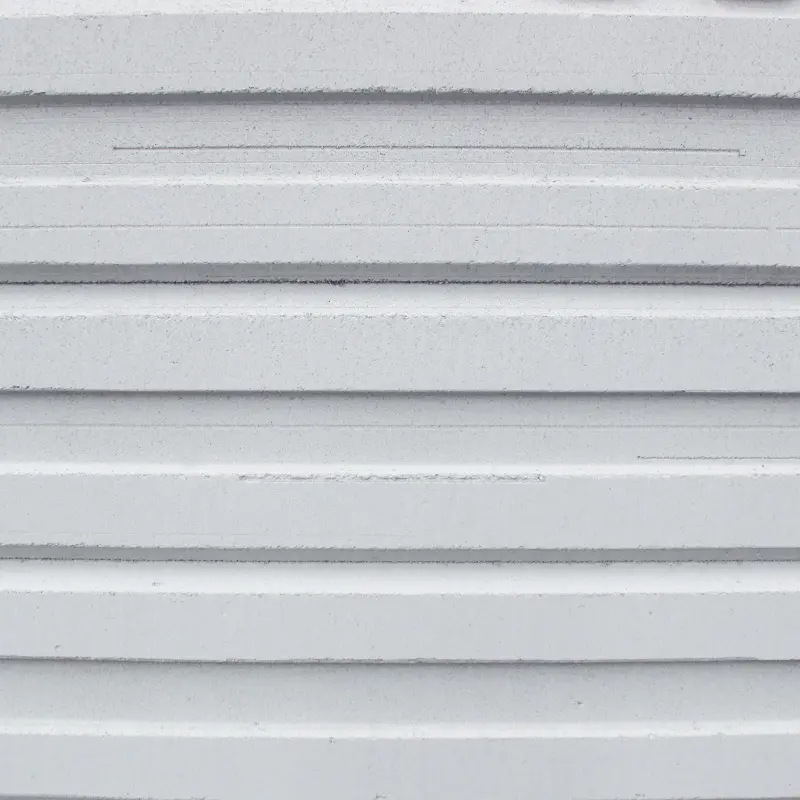
8. How Do AAC Blocks Influence Construction Speed and Overall Project Costs?
One of the most significant practical advantages of AAC blocks is their positive impact on construction timelines and budgets. The larger size of AAC blocks compared to traditional lpar;bricks) means walls go up much faster. A single AAC block can cover the area of 8-10 standard clay bricks. This translates directly into reduced labor hours for masonry work.
The dimensional accuracy of AAC blocks allows for the use of thin-bed mortar, which sets faster and requires less volume than conventional mortar. This not only saves material costs but also speeds up the layering process. Furthermore, the ease of workability – cutting, chasing, and shaping AAC blocks – simplifies the work of electricians, plumbers, and finishing trades, reducing overall construction time.
While the upfront cost per AAC block might seem higher than a single brick, the overall project cost is often lower. Savings accrue from:
- Reduced Labor: Faster installation means fewer man-hours.
- Reduced Mortar: Thin-bed mortar significantly cuts down on cement and sand usage.
- Structural Savings: The lightweight nature reduces the dead load, potentially allowing for smaller foundations and less reinforcing steel in the structure, resulting in significant savings.
- Reduced Finishing Costs: Precise dimensions mean thinner plaster coats are needed.
- Transportation Savings: More square meters of wall can be transported per truckload due to the lower weight.
- Long-Term Energy Savings: The inherent thermal insulation drastically cuts heating and cooling costs over the building’s lifespan.
Therefore, when considering the total cost of construction – including materials, labor, structural components, time, and long-term operational expenses – AAC blocks frequently emerge as a more economical choice than traditional brick or concrete block construction.
9. Sourcing High-Quality AAC: What Factors Matter Most for Blocks and Raw Materials?
Ensuring the quality of AAC blocks is paramount for the structural integrity, performance, and longevity of a building. When sourcing AAC blocks, or the raw materials like aluminum paste needed for their production, several factors are crucial, resonating with the concerns of discerning buyers like Mark Thompson:
- Consistency in Quality: Look for suppliers who demonstrate rigorous quality control throughout their manufacturing process. This includes consistent raw material sourcing, precise batching, controlled expansion, accurate cutting, and uniform autoclave curing. Inconsistent quality, especially in the aluminum powder or paste used, can lead to variations in density, strength, and permeability of the final AAC block. For manufacturers of AAC, sourcing Aluminium pastes for aerated concrete from reliable factories with years with good reputation. is critical for predictable gas generation and product quality.
- Compressive Strength: Verify that the AAC blocks meet the required compressive strength specifications for the intended application (e.g., load-bearing vs. non-load-bearing walls). Reputable manufacturers provide certified test reports. Strength typically ranges from 2.5 N/mm² to 7 N/mm².
- Dimensional Accuracy: Blocks should have precise dimensions with minimal tolerances (+/- 1-2 mm). This ensures ease of installation, level walls, and optimal performance with thin-bed mortar.
- Density: The density should be consistent and match the specified grade (e.g., 550-650 kg/m³). Density impacts weight, insulation, and strength.
- Certifications and Compliance: Ensure the supplier and their products meet relevant industry standards (e.g., ASTM C1693 in the USA, EN 771-4 in Europe) and possess necessary certifications (like ISO 9001 for quality management). Compliance with local building codes is non-negotiable. Material Safety Data Sheets (MSDS) should also be available.
- Moisture Content: Properly cured AAC blocks should have a low residual moisture content upon delivery. High moisture can affect initial adhesion and long-term performance.
- Packaging and Logistics: Due to their size and relative brittleness compared to dense concrete, AAC blocks require proper packaging (e.g., strapped on pallets, shrink-wrapped) to minimize damage during transport and handling. Reliable logistics are crucial to avoid construction delays.
- Supplier Reliability and Communication: Choose suppliers with a proven track record, transparent communication, and good customer support. Efficient communication is key to resolving potential issues quickly and managing procurement effectively – a common pain point for international buyers. As a Professional Water-based Aluminum Powder Slurry Factory, we understand the importance of consistency and reliability for downstream AAC block producers.
Focusing on these factors helps ensure you procure high-quality AAC blocks or the essential raw materials, leading to successful and durable construction projects.
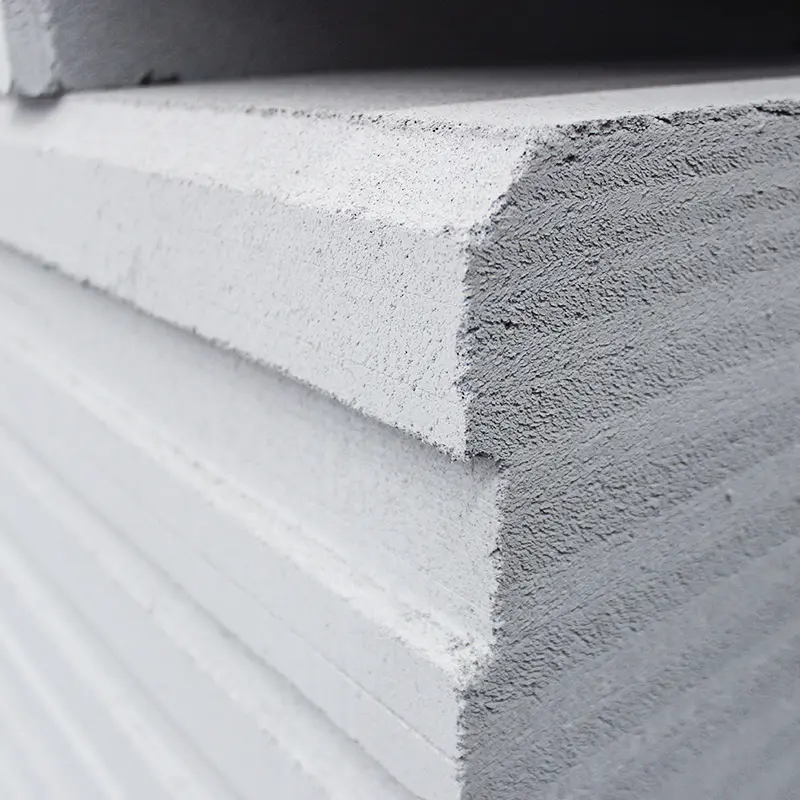
10. Why are AAC Blocks Seen as a Sustainable and Eco-Friendly Building Material Choice?
In an era increasingly focused on sustainable construction practices, AAC blocks stand out as an environmentally conscious choice for several reasons:
- Resource Efficiency: AAC blocks require fewer raw materials per cubic meter compared to dense concrete or brick. Furthermore, a key ingredient can be fly ash, an industrial byproduct from coal-fired power plants. Utilizing fly ash reduces landfill waste and the need to quarry virgin materials like quartz sand.
- Lower Embodied Energy: While the autoclave process requires energy, the overall manufacturing energy consumption for AAC blocks can be lower than that for producing traditional clay bricks, which require high-temperature firing for extended periods. The lightweight nature also reduces transportation energy.
- Superior Energy Performance: This is perhaps the most significant sustainability advantage. The excellent thermal insulation provided by AAC blocks dramatically reduces the energy required for heating and cooling buildings throughout their operational life. This leads to lower greenhouse gas emissions and reduced reliance on fossil fuels.
- Reduced Waste: The precise dimensions of AAC blocks minimize mortar usage and wastage. The workability allows off-cuts to be easily reused for smaller infill areas, further reducing site waste compared to traditional methods. The material itself is non-toxic and does not release harmful pollutants.
- Durability and Longevity: AAC blocks create durable buildings that last for decades, reducing the need for frequent repairs or reconstruction, thus conserving resources over the long term. They are resistant to pests, mold, and rot.
- Non-Biodegradable but Inert: While non-biodegradable, AAC is chemically inert and does not leach harmful substances into the soil or water. Manufacturing scraps can often be recycled back into the production process.
These factors combined make Autoclaved Aerated Concrete (AAC block) a preferred new building material for green building projects and sustainable development initiatives worldwide. Its contribution to energy efficiency, resource conservation, and waste reduction aligns well with the goals of environmentally responsible construction. Companies looking for reliable, sustainable solutions often turn to materials like AAC blocks and the structurally capable ALC Wallboard for their projects.
Key Takeaways About AAC Blocks:
- AAC stands for Autoclaved Aerated Concrete, a lightweight, precast foam concrete block.
- Manufactured using cement, lime, sand/fly ash, water, and aluminum powder, then cured in an autoclave.
- Significantly lighter than traditional brick or concrete blocks, reducing structural load.
- Offers excellent thermal insulation, leading to substantial energy savings.
- Provides superior fire resistance compared to many other construction materials.
- Good acoustic insulation properties contribute to quieter buildings.
- Larger size and dimensional accuracy speed up construction and reduce mortar consumption.
- Highly workable, easy to cut, drill, and shape on site.
- Considered a sustainable building material due to resource efficiency and energy performance.
- Requires protective finishing for exterior wall applications and care during handling.
- Quality control in manufacturing (especially consistency from the autoclave process and raw materials) and proper installation are crucial for optimal performance.
AAC blocks represent a modern, efficient, and sustainable approach to masonry construction, offering compelling advantages for a wide range of building projects.
Post time: 4 月-08-2025