Aluminum paste is a remarkable and versatile material that powers innovation across dozens of industries, from the shimmering finish on a new car to the structural integrity of modern, energy-efficient buildings. For business owners and procurement officers like you, understanding the nuances of this metallic pigment is not just a matter of chemistry; it’s a matter of profitability, product quality, and project success. This guide is written from my first-hand experience as a factory owner specializing in this very field. We will demystify aluminum paste, explore its diverse applications, and provide the critical insights you need to source the best materials for your business, ensuring you avoid common pitfalls like quality inconsistency and shipment delays.
1. What Exactly Is Aluminum Paste and How Is It Made?
At its core, aluminum paste is a specialized pigment composition. It consists of millions of microscopic flake-like particles of aluminum suspended in a carrier medium, which is typically a solvent or water. Think of it not as a simple mixture but as a highly engineered dispersion. The primary goal is to take a solid metal, aluminum, and transform it into a format that can be easily incorporated into other products like paint, coatings, or even concrete slurries. The final paste has a thick, viscous consistency, similar to a very fine, metallic silver-grey mud.
The production process is a critical factor that dictates the quality and performance of the final paste. It begins with high-purity raw materials, specifically aluminum atomized powder. This powder is loaded into large rotating cylinders called ball mills, along with a specific lubricant (often a fatty acid like stearic acid) and a solvent. Inside the mill, steel balls cascade and grind the aluminum powder, flattening the particles into the desired microscopic flakes. This milling process is carefully controlled to achieve a specific particle size distribution, which is crucial for the final application.
After the milling is complete, the resulting slurry is filtered to remove the grinding media, and the concentration of aluminium flakes is adjusted to meet specification. The choice of solvent is also critical; it can range from aromatic hydrocarbons to mineral spirits or, in more modern formulations, a water-based system. The entire process requires precision engineering to ensure every batch of aluminium paste has consistent properties.
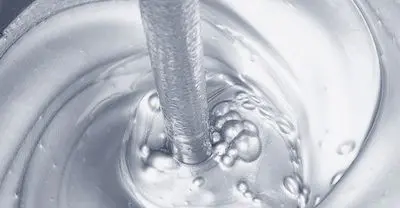
2. What Are the Key Properties of Aluminum That Make It Ideal for Pastes?
Aluminum is not chosen by accident for these applications. The inherent properties of aluminum make it uniquely suited for creating high-performance pigment pastes. Firstly, its excellent ductility is what allows it to be flattened into ultra-thin flakes during the milling process without fracturing. These flakes are the foundation of the paste‘s functionality. Secondly, aluminum is incredibly lightweight, which is a benefit when incorporated into a coating or, more significantly, when used to create light weight concrete.
Furthermore, aluminum possesses excellent reflective properties. The tiny flakes act as miniature mirrors, reflecting a significant amount of light and heat. This property is responsible for the brilliant metallic sheen in decorative paints and is also vital for protective coatings designed to reflect solar radiation away from the surface. This thermal reflectivity also contributes to its role in insulation. The metal also has good conductivity, which is leveraged in certain specialized applications, such as conductive inks or coatings for electronics where heat dissipation is required.
Another key property is its ability to react with certain chemicals. While this can be a challenge (as it can be explosive under the wrong conditions), this reactivity is precisely what is harnessed in applications like autoclaved aerated concrete. When the aluminum paste is mixed into a slurry with lime and cement, it reacts to produce hydrogen gas, creating the millions of tiny air pockets that give the material its lightweight and insulative properties. This controlled chemical reaction is a perfect example of leveraging the fundamental properties of aluminum for an industrial purpose.
3. Leafing vs. Non-Leafing Aluminum Paste: What’s the Real Difference?
When you delve into the world of aluminum paste, you will immediately encounter the terms "leafing" and "non-leafing." These terms describe the behavior of the aluminum flakes once the paste is applied within a coating or paint. The difference is created during the manufacturing process, primarily by the choice of lubricant, like stearic acid, used during milling. Understanding this distinction is crucial for selecting the right paste for your application.
Leafing and non-leafing behavior is all about the orientation of the aluminum flakes within the dried film of paint or coating.
-
Leafing pigments: In a leafing aluminium paste, the flakes are coated with a fatty acid that is largely insoluble in the paint‘s solvent system. This causes the flakes to rise to the surface of the wet film and align themselves parallel to the surface, overlapping like fallen leaves on water. This creates a brilliant, chrome-like, highly reflective finish. Leafing pigments provide excellent opacity, or good hiding power, and superior protection against moisture and UV radiation because they form a near-continuous metallic barrier on the substrate.
-
Non-leafing pigments: With a non-leafing aluminum paste, the flakes are treated with a different type of fatty acid that promotes "wetting" by the resin system of the paint. As a result, the flakes remain dispersed and distributed evenly throughout the entire depth of the coating film, rather than floating to the top. This results in a more subdued, satin-like metallic effect. The primary advantage of non-leafing grades is that the coating can be easily tinted with other pigments and can be recoated without adhesion issues, which can be a problem with the slick surface created by leafing pigments.
The choice between them is application-driven. For a highly reflective roof coating or a corrosion-resistant industrial paint, a leafing paste is ideal. For an automotive basecoat that will be covered by a clear topcoat, or a plastic part with a subtle metallic effect, a non-leafing paste is the correct choice.
4. Why Is Water-Based Aluminum Paste Gaining Popularity?
For decades, the standard in the paints and coatings industry was solvent-based aluminum paste. The use of solvents like mineral spirits or aromatic hydrocarbons was effective for dispersing the aluminium flakes. However, growing environmental regulations and a global push towards sustainability have dramatically increased the demand for water-based alternatives. As a factory, we have invested heavily in our water-based production lines because we see this as the future.
The primary driver is the reduction of Volatile Organic Compounds (VOCs). Traditional solvents evaporate into the atmosphere during the drying process, contributing to air pollution and posing health risks to workers. A water-based aluminium paste replaces the vast majority of this organic solvent with water, making it a much cleaner and safer technology. This is particularly important for customers in Europe and North America, where environmental standards are increasingly strict. This shift helps our customers meet regulatory requirements and market their end-products as "eco-friendly."
However, creating a stable and effective water-based paste presents technical challenges. Aluminum naturally reacts with water to produce hydrogen gas. To prevent this, the aluminum flakes in a water-based paste must be specially treated and encapsulated with an inhibitor layer, often a silica-based or polymer coating. This passivation process is complex and requires a high degree of technical expertise to ensure the long-term stability and performance of the paste. The result is an aqueous paste that offers the same brilliant metallic effects as its solvent-based counterparts but with a significantly smaller environmental footprint.
5. How Does Aluminum Paste Create That Stunning Metallic Coating?
The beautiful, shimmering metallic finish you see on cars, electronics, and high-end packaging is a direct result of the physics of aluminum paste. The magic lies in the shape and orientation of the millions of flake-like particles suspended in the coating. When you spray or apply a paint containing this paste, these flakes align themselves in a specific way as the solvent or water evaporates.
In a well-formulated coating, the flakes arrange themselves in layers parallel to the substrate. Each individual flake acts as a tiny mirror. When light strikes the surface, it doesn’t just reflect off the top layer. It penetrates slightly, reflecting off multiple layers of flakes at different depths. This multi-layered reflection is what creates the deep, lustrous, and eye-catching metallic sheen that a simple grey paint could never replicate. The brilliance of the effect is directly related to the quality of the aluminum paste—specifically, the smoothness of the flake surfaces and the narrowness of the particle size distribution.
The type of paste also dictates the final look. Leafing pigments, as discussed, create a bright, chrome-like surface by concentrating at the very top of the coating. Non-leafing pigments are distributed throughout the film, resulting in a "depth" to the metallic effect, where the sparkle seems to come from within the paint itself. This is why non-leafing types are preferred in the automotive industry for basecoats, as they create a rich finish that is then protected and enhanced by a clear topcoat. It’s this precise control over light that allows aluminum paste to add a touch of luxury and sophistication to countless products.
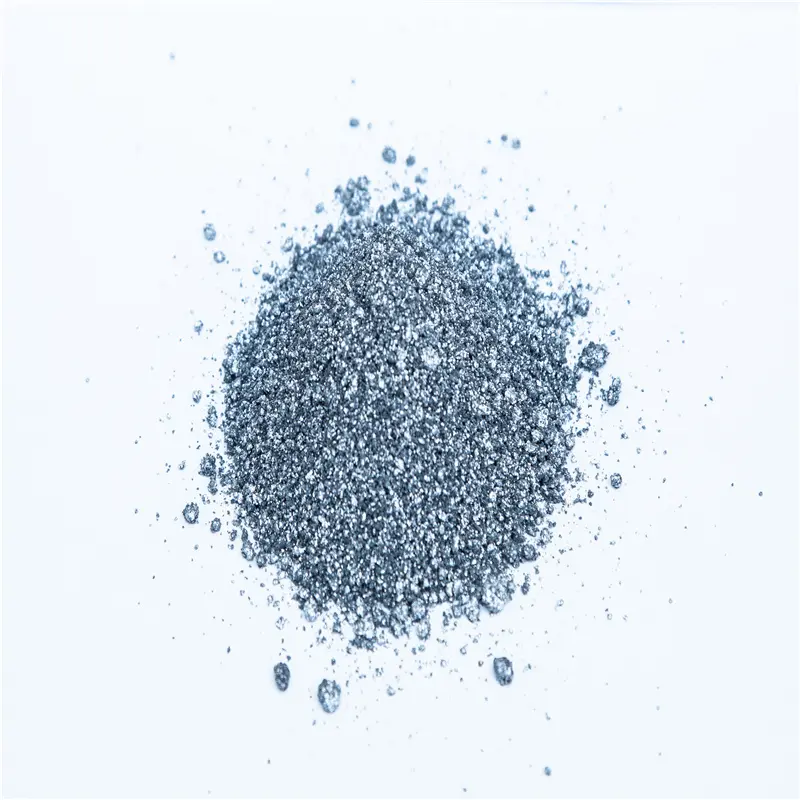
6. What Are the Primary Applications of Aluminum Paste in the Coatings Industry?
The coatings industry is the largest consumer of aluminum paste, where its uses are both functional and decorative. The versatility of the paste allows it to be incorporated into a vast range of products, from industrial primers to high-end automotive finishes. The specific grade of aluminium paste is selected based on the desired appearance and performance requirements of the final coating.
Here’s a breakdown of key applications:
- Automotive Industry: This is a huge market. Non-leafing aluminum paste is essential for car paints, providing the metallic sparkle in basecoats. Different flake sizes are used to create effects from fine, silky sheens to coarse, glittery finishes. The paste must have excellent adhesion and be compatible with the complex resin systems used in automotive paint.
- Protective & Industrial Coatings: For applications like bridges, storage tanks, and pipelines, leafing aluminum paste is used to create highly durable protective coatings. The overlapping flakes form a barrier that shields the underlying substrate from moisture, corrosion, and UV degradation. The high reflectivity also helps to reduce heat absorption.
- Plastics and Consumer Electronics: The demand for metallic finishes on plastic casings for laptops, phones, and home appliances is immense. A fine-grade aluminum paste is mixed directly into the plastic or used in a coating applied to the surface to give a premium look and feel.
- Printing Inks: In the packaging and printing world, aluminum paste is used to create metallic ink. This is used for high-end labels, flexible packaging, and magazines to create eye-catching graphics and text that stand out on the shelf. The ink formulation requires a very fine pigment for sharp, clean printing.
7. Can Aluminum Paste Be Used Beyond Decorative Coatings?
Absolutely. While the paints and coatings industry is its biggest market, the unique properties of aluminum paste have led to its adoption in a wide range of other industrial applications. These uses often leverage the functional, rather than aesthetic, characteristics of the aluminum flakes. From construction to renewable energy, aluminum paste offers solutions to unique engineering challenges.
For instance, the thermal conductivity of aluminum is utilized in specialized adhesives and sealants. By incorporating aluminum paste, these materials can help in the dissipation of heat, which is crucial in electronic assemblies. Similarly, its electrical conductivity makes it a component in certain conductive inks and coatings used for printed circuits or antistatic flooring. In the aerospace industry, lightweight, reflective coatings containing aluminum paste are used on certain components to manage thermal loads.
Another fascinating application is in the manufacturing of solar panels. Specific types of aluminum paste are used to print the rear-side contact on crystalline silicon solar cells. This printed layer acts as a conductor, collecting the electrons generated when sunlight strikes the cell. In this high-tech application, the quality of the paste—its dispersion process, purity, and particle characteristics—directly impacts the efficiency and lifespan of the solar panel. These applications demonstrate that aluminum paste plays a crucial role well beyond just making things look good.
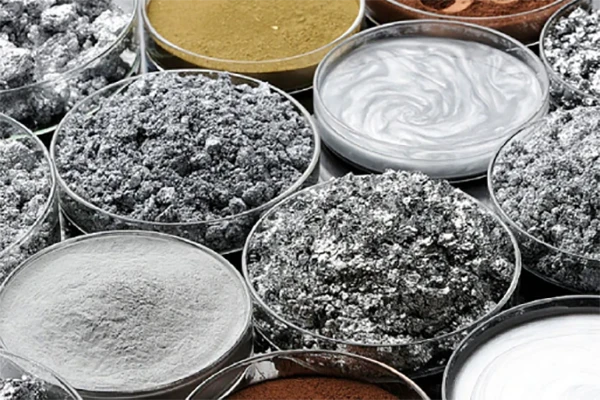
8. How Does Aluminum Paste Play a Crucial Role in Autoclaved Aerated Concrete (AAC)?
This is an area of deep expertise for my factory and a perfect example of a functional application. In the production of Autoclaved Aerated Concrete (AAC) and its related products, aluminum paste is not a pigment for color; it’s a chemical gas-forming agent. The paste plays a crucial role in creating the material’s signature lightweight, cellular structure. This is one of the most important uses of aluminum paste in the modern construction industry.
The process is fascinating. A slurry is made from fine-ground sand, lime, cement, and water. A very small, precisely measured amount of a specialized water-based aluminium paste is then added. The alkaline environment of the slurry triggers a chemical reaction with the aluminum particles, releasing millions of microscopic bubbles of hydrogen gas. This is similar to how baking powder makes a cake rise. The slurry expands within its mold, creating a "cake" of what will become light weight concrete. The material is then cut into blocks or panels and cured in a high-pressure autoclave (a large steam chamber), which hardens it into its final, structurally stable form.
The quality of the aluminium paste for aerated concrete is paramount. The reaction rate must be perfectly controlled. If it’s too fast, the gas escapes before the mixture sets. Too slow, and the desired density isn’t achieved. That’s why customers like Mark Thompson, who manufacture precast concrete, rely on suppliers who can guarantee consistent particle size distribution and reactivity. This ensures that every batch of concrete has uniform strength and insulation properties. This technology is the foundation for high-performance building materials like lightweight AAC Block and reinforced ALC Wallboard, which are prized for their excellent thermal insulation, fire resistance, and ease of use.
9. What Should You Look for When Sourcing High-Quality Aluminium Paste from a Factory?
For a procurement officer like Mark, sourcing aluminium paste from an overseas factory can be daunting. The right choice can lead to a reliable supply chain and superior products, while the wrong one can cause production nightmares and project delays. Based on my experience working with hundreds of B2B clients, here are the critical factors to consider:
Concern | What to Look For in a Supplier |
---|---|
Quality Consistency | Ask for batch-to-batch test reports. A good factory will provide Certificates of Analysis (CoA) for every shipment, detailing particle size, non-volatile content, and performance tests (like gas generation for AAC paste). Consistency is more important than a single "golden sample." |
Technical Expertise & Communication | Your contact should be more than a salesperson. They should be able to discuss technical details, like the difference between leafing and non-leafing grades or the ideal formulation for your specific coating or AAC density. Clear, prompt communication in English is non-negotiable. |
Certifications | Look for ISO 9001 certification, which indicates a robust quality management system. Ask for Material Safety Data Sheets (MSDS) and check for compliance with any relevant standards in your country (e.g., ASTM standards in the USA). |
Logistics & Packaging | This is a major pain point. Discuss packaging options to prevent damage, especially for a paste product. A professional factory will have experience with international shipping protocols, providing robust packaging and clear documentation to avoid customs delays. Ask about their track record for on-time delivery. |
Factory Transparency | Are they a trading company or a true factory? A real factory, like our professional water-based aluminum powder slurry factory, will be happy to show you their production lines (even via video tour), discuss their capacity, and explain their quality control process from raw materials to final product. |
As an owner, I’ve seen firsthand how a breakdown in any of these areas can halt a customer’s production line. A reliable supplier isn’t just selling you a drum of paste; they are selling you peace of mind and a partnership in quality. Don’t be afraid to ask tough questions about their processes.
10. The Future of Aluminum Paste: Innovations and Trends to Watch
The world of aluminum paste is not static. Innovation is constantly driven by new regulations, market demands, and technological advancements. As we look to the future, several key trends are shaping the industry. One of the biggest is the continued development of high-performance water-based systems. The challenge is not just to replace the solvent but to create aqueous pigment pastes that match or even exceed the brilliance and durability of their solvent-borne predecessors, especially for demanding applications like automotive coatings.
Another area of innovation is in particle morphology. Researchers and manufacturers are experimenting with new milling techniques and additive packages to create flakes with smoother surfaces, thinner profiles, and even different shapes. This research aims to create new visual effects, such as "chrome-like" coatings that are more environmentally friendly than traditional chrome plating, or finishes that can change color depending on the viewing angle. This includes creating more specialized non-leafing pigments for unique aesthetic effects in plastic and ink.
Finally, there’s a growing focus on sustainability throughout the entire lifecycle. This includes using recycled aluminum as a raw material, reducing energy consumption during the milling process, and developing pastes that contribute to the longevity and energy efficiency of the products they’re used in. For example, enhancing the reflectivity of an aluminium paste for roof coatings can lower building energy costs, while optimizing the gassing reaction in an AAC paste reduces material waste. The future of technical aluminium paste is cleaner, more efficient, and more versatile than ever before.
Key Takeaways to Remember
- Aluminum Paste is Versatile: It’s a highly engineered pigment used for both stunning metallic aesthetics in the coatings industry and critical functional roles, like acting as a gas-forming agent in autoclaved aerated concrete (AAC).
- Leafing vs. Non-Leafing is Crucial: Leafing flakes float to the surface for a bright, chrome-like protective coating, while non-leafing flakes disperse throughout the film for a deep, satin metallic effect suitable for automotive basecoats.
- Water-Based is the Future: Driven by environmental regulations, water-based aluminium paste is replacing traditional solvent-based products, offering a safer and more sustainable solution without compromising performance.
- Application Dictates the Choice: The right paste depends entirely on the end use, whether it’s for paint, ink, plastic, or creating lightweight building materials like AAC blocks and ALC panels.
- Sourcing Requires Diligence: When choosing a supplier, prioritize quality consistency, technical expertise, proper certifications (ISO, MSDS), and proven logistics capabilities to avoid common B2B purchasing pain points. A true factory partner will be transparent about their production process.
Post time: 6 月-17-2025