Welcome to a deep dive into the world of aluminum powder. You’ve likely encountered its applications in everyday life, from shiny paints to advanced construction materials. But this versatile material holds a hidden power that demands respect and understanding. As a factory owner, Allen, with seven production lines dedicated to building materials, I’ve worked with aluminum for years, particularly in creating high-quality pastes for aerated concrete. This article is born from that experience. We will explore the properties of aluminum powder, its critical role in industries, and most importantly, the safety protocols necessary to handle it. If you’re a procurement officer like Mark Thompson, a construction company owner, or a building materials distributor, understanding these aspects is not just about compliance—it’s about ensuring safety, quality, and operational success. This guide will provide you with the essential knowledge to make informed decisions and handle this potent metal powder with the expertise it requires.
What Exactly Is Aluminum Powder and How Is It Made?
Aluminum powder is essentially aluminum metal that has been processed into a fine, granular form. Think of it as flour, but made of a highly reactive metal. The production process typically involves melting high-purity aluminum ingots and then atomizing them. In atomization, a stream of molten metal is broken up by high-pressure jets of air or an inert gas (like nitrogen). This scatters the liquid metal into tiny droplets that solidify into a fine powder as they cool. The resulting particle shape can be controlled during this process, often resulting in a spherical or irregular shape depending on the end-use requirements.
The characteristics of the final powder are heavily influenced by the manufacturing process. Factors like the cooling rate and the atomizing gas determine the particle size distribution, which is a critical parameter. A finer powder with a smaller particle size (often measured in micron or μm) has a vastly larger surface area per unit of mass. This increased surface area is what makes the powder so useful in chemical reactions but also significantly increases its reactivity and potential hazard. In our factory, we grind and carefully control the particle size to ensure consistent performance in our products, from pigments to the specialized aluminium pastes for aerated concrete.
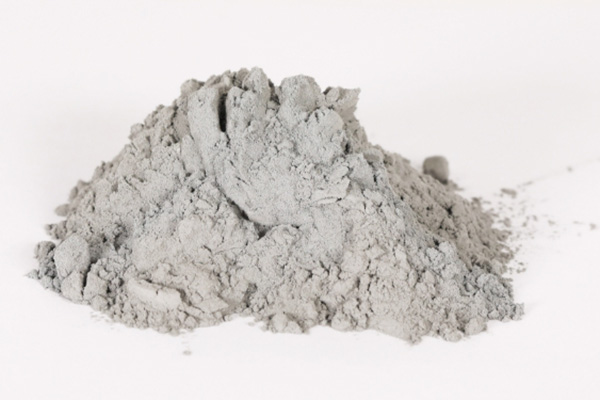
Why is Finely Divided Aluminum Powder a Significant Hazard?
The primary hazard associated with finely divided aluminum powder is its potential for a violent fire or explosion. This risk stems directly from its physical properties. A solid block of aluminum is relatively safe; you can hold it, heat it, and it won’t easily burn. However, when you break that same block down into billions of tiny particles, you dramatically increase the surface area exposed to oxygen. This high surface area makes the powder much more reactive and easier to ignite.
When this powder is dispersed in the air, it can form a combustible dust cloud. If this cloud encounters an ignition source, the result can be a devastating explosion. The combustion wave can travel through the cloud at incredible speeds, generating immense pressure and heat, which can lead to property damage, severe injuries, or fatalities. This is why any facility that handles powdered aluminum must treat it with extreme caution. The risk is not theoretical; industrial history is filled with examples of dust explosions, and aluminum is one of the most significant metallic dust hazards.
How Does Aluminum Powder React with Water to Produce Hydrogen Gas?
One of the most critical chemical properties of aluminum is its reaction with water. While a solid piece of aluminum appears unreactive in water due to a protective oxide layer, aluminum powder behaves very differently. The fine particles can react with water (H₂O) in a chemical reaction to produce hydrogen gas (H₂) and aluminum oxide. This reaction is exothermic, meaning it releases heat, which can further accelerate the reaction. The equation looks like this:
2Al (s) + 3H₂O (l) → Al₂O₃ (s) + 3H₂ (g) + Heat
This very reaction is harnessed in the construction industry to create aerated concrete. In our Aluminium pastes for aerated concrete, we control this reaction precisely. The aluminum powder reacts with water and lime in the concrete mixture to generate tiny hydrogen gas bubbles. These bubbles create a lightweight, insulating structure within the concrete, resulting in products like our durable AAC Blocks. However, outside of this controlled process, the uncontrolled production of hydrogen is an extreme hazard. Hydrogen is a highly flammable gas that can form an explosive mixture with air. If hydrogen could accumulate in a poorly ventilated area, even a small spark could trigger a dangerous explosion.
What are the Main Ignition Sources for an Aluminum Powder Explosion?
For an aluminum powder explosion to occur, two primary components are needed: a dispersed cloud of powder at the right concentration and an ignition source. Identifying and controlling potential ignition sources is a cornerstone of safety. The ignition energy required to set off an aluminum dust cloud can be surprisingly low.
Common ignition sources include:
- Open Flames: Welding torches, pilot lights, or even a lit cigarette can easily ignite a dust cloud.
- Sparks:
- Mechanical Sparks: Generated from friction, such as a tool striking a metal surface. Using non-sparking tools made of materials like copper or brass is crucial.
- Electrical Sparks: Faulty wiring, unrated electrical components, or the normal operation of switches and motors can create sparks. All electrical equipment in hazardous areas must be rated for dust-explosive atmospheres.
- Static Electricity: The movement and handling of powder can generate significant static charge. If this charge is not safely grounded, it can discharge as a spark with enough energy to cause an ignition. Proper bonding and grounding of all equipment are essential to dissipate this charge.
- Hot Surfaces: Overheated bearings, motors, or even hot light fixtures can reach temperatures high enough to ignite accumulated aluminum dust.
As a manufacturer, I always advise clients like Mark to conduct a thorough hazard analysis of their facilities. You must assume that a dust cloud could form and focus relentlessly on eliminating every potential ignition source.
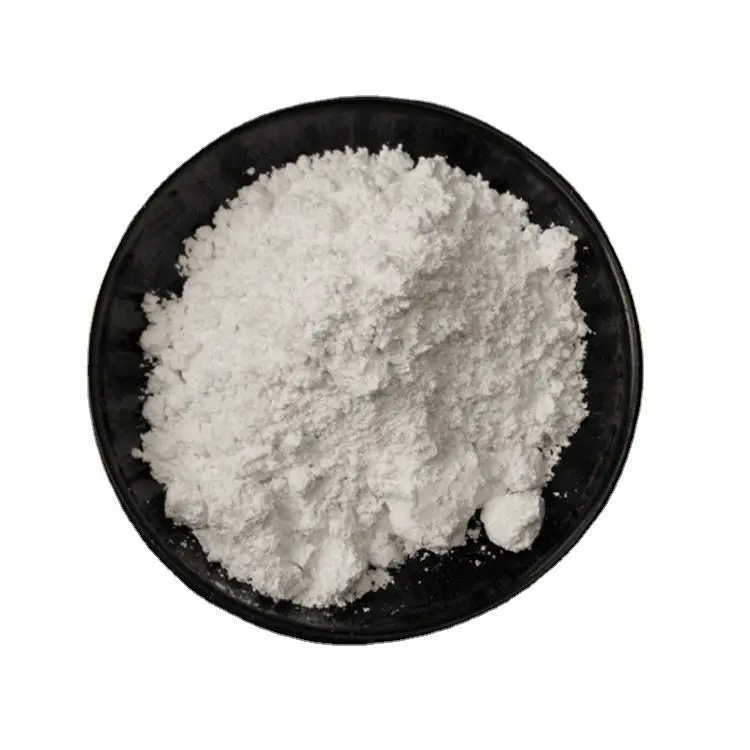
Can Aluminum Powder Spontaneously Ignite? The Role of the Oxide Layer
The idea of a material bursting into flame without an external ignition source is alarming, and with aluminum powder, it’s a possibility under certain conditions. This phenomenon is closely tied to the protective oxide layer that naturally forms on the surface of aluminum. This incredibly thin layer of aluminum oxide (Al₂O₃) is what normally prevents the metal from reacting with its environment, including the oxygen in the air. It acts as a passive shield.
However, if this oxide layer is damaged or if the powder is extremely fine (increasing reactivity), the raw aluminum metal can begin to oxidize rapidly. This oxidation process is exothermic, releasing heat. If this heat is generated faster than it can dissipate into the surroundings—for example, in a large, unventilated pile of powder—the temperature can rise to the point of self-ignition. The presence of contamination, such as moisture (moist air) or other reactive chemicals, can accelerate this process and increase the probability of an accident. This underscores the importance of proper storage and ensuring the powder is kept dry and free from any impurity.
What is a Dust Explosion and How Does it Apply to Aluminum Powder?
A dust explosion is a rapid combustion of fine particles suspended in air in an enclosed location. For this to happen, five elements, often called the "Dust Explosion Pentagon," must be present:
- Fuel: Combustible dust (like aluminum powder)
- Oxidizer: Oxygen in the air
- Ignition Source: A spark, flame, or hot surface
- Dispersion: The dust must be suspended in the air at a sufficient concentration.
- Confinement: The explosion is most destructive in an enclosed space, like a room or a piece of equipment, where pressure can build.
When an ignition occurs in a dust cloud, the flame front races from one particle to the next, creating a massive and nearly instantaneous release of energy. This creates a high-pressure wave that can destroy buildings and equipment. A particularly dangerous aspect is the risk of a secondary explosion. An initial, smaller explosion can dislodge more dust that has settled on surfaces, creating a much larger and more destructive secondary dust cloud that then ignites. This is why good housekeeping to prevent dust accumulation is a life-or-death matter. A thin layer of dust, seemingly harmless, can become the fuel for a catastrophic event.
What Regulatory Standards (like NFPA) Govern the Handling of Aluminum?
Given the significant hazards, the handling of aluminum powder is strictly regulated. In the United States, the National Fire Protection Association (NFPA) provides the most critical standards. Several NFPA codes are relevant, but the most important one is NFPA 652, Standard on the Fundamentals of Combustible Dust. This standard establishes the baseline requirements for managing combustible dust fire hazards and explosions across all industries.
Furthermore, NFPA 484, Standard for Combustible Metals, provides specific and detailed guidance for metals like aluminum, magnesium, and titanium. These standards cover everything from building construction and equipment design to dust collection systems, housekeeping procedures, and employee training. Compliance with NFPA standards is often required by local fire codes and insurance carriers. For a company owner like Mark, verifying that a supplier understands and adheres to principles outlined in these regulatory frameworks is a crucial step in vetting a partner. It demonstrates a commitment to safety that goes beyond just selling a product. At our company, BTZmoc, we engineer our processes with these global standards in mind, ensuring the safety of our team and the reliability of our products.
NFPA Guideline Area | Key Recommendation for Aluminum Powder Handling |
---|---|
Dust Control | Use dust collection systems designed to prevent explosion propagation. |
Ignition Source Control | Implement strict controls on open flames, welding, and smoking. Use properly rated electrical equipment. |
Housekeeping | Regularly clean all surfaces to prevent any fugitive dust accumulation. |
Grounding & Bonding | All equipment, containers, and personnel must be grounded to prevent static discharge. |
Explosion Protection | Use explosion suppression systems, isolation devices, or explosion vent panels on equipment. |
How Can You Safely Handle and Store Aluminum Powder to Mitigate Risks?
Safe handling and storage are non-negotiable. It starts with a mindset of prevention. Every step, from receiving a shipment to using the powder in a process, must be carefully planned. During transport, containers must be robust, sealed, and clearly labeled as hazardous material. Upon receipt, inspect containers for any damage.
For storage, aluminum powder should be kept in a cool, dry, well-ventilated area, away from incompatible materials like acids, bases, and oxidizers. The storage area should be a detached building or a room with fire-resistant construction. Water is a major enemy; the storage area must be protected from rain, sprinklers (unless a specific Class D system is in place), and any other sources of moisture. Use a waterproof tarp for temporary covering if needed. All handling should be done with non-sparking tools, and personnel should wear appropriate personal protective equipment (PPE), including flame-retardant clothing and respiratory protection. Preventing dust clouds from forming is key, so handle the powder gently and use ventilation systems to capture any fugitive dust at the source before it can accumulate.
What are the Fire-Fighting Procedures for an Aluminum Metal Fire?
Fighting an aluminum metal fire is completely different from fighting a typical fire. Never use water, foam, or carbon dioxide (CO₂) extinguishers. Applying water will cause a violent reaction, releasing explosive hydrogen gas and making the situation far worse. Carbon dioxide can also react with burning aluminum. This is a Class D fire, and it requires a Class D fire extinguisher.
The correct procedure is to gently smother the fire. Use a Class D extinguishing agent, which is typically a dry powder like G-1 (graphite) or Met-L-X (sodium chloride-based). These agents work by forming a crust over the burning metal, cutting off the oxygen supply and allowing it to cool. If a Class D extinguisher isn’t available, dry sand, soda ash, or limestone can be used to carefully cover and suffocate the fire. The key is to apply the agent gently to avoid disturbing the burning powder and creating a dust cloud. All personnel working with aluminum powder must be trained on this specific hazard and know the location and proper use of Class D extinguishers. An accident investigation of many industrial fires has shown that using the wrong extinguisher is a common and tragic mistake.
Choosing a Reliable Supplier: Why Quality and Consistency in Aluminum Powder Matter
For a procurement officer, the choice of supplier is paramount. While price is a factor, quality and consistency are where true value lies, especially with a material as sensitive as aluminum powder. Inconsistent quality can directly lead to production problems and safety hazards. For instance, variations in particle size distribution can alter the rate of the hydrogen gas-forming reaction, leading to unpredictable results in the production of AAC blocks or lightweight ALC Wallboard. An inconsistent particle means inconsistent product quality.
A reliable supplier provides more than just a drum of powder. They provide confidence. This means:
- Strict Quality Control: Verifiable data sheets showing consistent particle size, purity, and low moisture content.
- Freedom from Contamination: Ensuring the powder is free from any impurity like iron or magnesium that could adversely affect its performance or safety. We test every batch to guarantee purity.
- Robust Packaging and Logistics: Secure packaging that prevents moisture absorption and damage during transport.
- Technical Support and Transparency: A partner who understands your application and can provide guidance on safe handling and use. This is the expertise we, as a specialized factory with 7 production lines, bring to our clients.
Ultimately, a quality aluminum powder ensures a predictable chemical reaction, a safe operating environment, and a superior final product. It’s an investment in reliability and safety that pays dividends long after the invoice is settled.
Key Takeaways to Remember
- Aluminum powder is a significant hazard. Its fine particle size makes it highly reactive and creates a serious risk of fire or explosion.
- Water is a dangerous reactant. Aluminum powder reacts with water to produce highly flammable hydrogen gas. Never use water to fight an aluminum fire.
- Control dust and ignition sources. The "Dust Explosion Pentagon" teaches us that preventing dust clouds and eliminating sparks, flames, and static is critical.
- Follow regulatory standards. Adherence to NFPA standards like 652 and 484 is essential for safe operation.
- Use the right tools. Always use Class D fire extinguishers for metal fires and non-sparking tools for handling.
- Supplier quality is safety. Choosing a reputable supplier that guarantees consistent particle size, purity, and proper packaging is fundamental to mitigating risk and ensuring product quality.
Post time: 7 月-08-2025